Feed-forward control of sludge dewatering
- Jo Wouters
- Feb 20
- 3 min read
Sludge type and concentration: "The crux of the matter"
As discussed in our previous post, sludge dewatering is a critical process in the wastewater treatment process. The main goal is to reduce the water content of sludge to facilitate easier handling, transportation, and disposal.
Sludge varies not only in total solids (TS) or dry solids (DS) concentration but also in the ratio of organic to inorganic content. In practice, one key distinction is between digested and non-digested sludge. Digested sludge is the product of aerobic or anaerobic digestion, processes that break down organic matter.
Digested sludge versus waste activated sludge
Digested sludge is the resultant material from either aerobic or anaerobic digestion. It is often black, homogeneous in nature and often supplied to dewatering plants in concentrations from 30-70 g/L. It can often be dewatered to a large extend in decanter centrifuges with the correct dosage of polyelectrolyte.
On the other hand, waste activated sludge can be supplied commonly to dewatering systems. Often it is the case for smaller wastewater treatment plants or when digester capacity is exceeded or digested sludge buffers are full. Waste activated sludge is often lower in feed concentration (25-50 g/L) and features larger sludge particle sizes. It is brown and settles rather quickly when stagnant.

The different sludge supply points in dewatering installations and fluctuations in concentration require an accurate measurement of sludge inlet flowrate and total solids content.
Due to the strongly fluctuating properties of waste and/or digested sludge, optical concentration sensors tend to fail to capture concentration gradients. Furthermore, above 50 g/L, optical sensors become rather unresponsive to changes in sludge concentration.
Operating at plant capacity
Decanter centrifuges, belt presses or filter presses operate best within their designed specifications of flowrate (L/h) and dry solids loading (kg/h). Let us consider the following trend in sludge concentration:
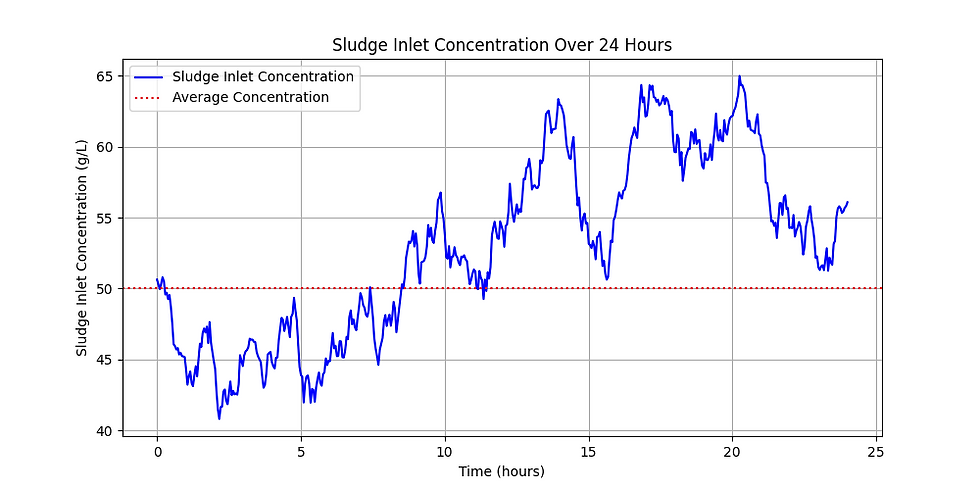
The average concentration of 50 g/L allows to define the flowrate of the dewatering plant to operate close to design specifcations. For example, operating at 8m³/h would put us at 8000L/h*0.050 kg/L = 400 kg/h. However, the inline concentration measurement directly implies that the solids loading can drop as low as 320 kg/h or above 500 kg/h.
Operating at constant flowrate implies highly variable solids loading on the plant.
Polyelectrolyte dosing in sludge dewatering
Constant flowrate operation implies that polyelectrolyte dosing needs to be varied in function of total solids loading.
Feed forward control of the dewatering plant allows to use sludge inlet concentration measurement to define the polymer dosage.
Coming back to the graph above, polymer dosage can be varied minute by minute to account for total solids concentration, implying a dosage increase of more than 30% from t=2h to t=20h.
Feed-forward control of sludge dewatering: Flowrate, solids loading and more
Feed-forward control of sludge dewatering allows automatic control of sludge feed flowrate and polyelectrolyte dosing.
Olpas sensors allow to measure sludge inlet concentration accurately with minimal maintenance, independent of sludge type. Feed-forward control of sludge dewatering is the first step towards optimizing and automating sludge dewatering:
It allows for fast and precise changes in polyelectrolyte/polymer dosing to the sludge inlet concentration.
Large changes in concentrations can be compensated for by sludge flowrate adjustments. It allows keeping the solids loading of systems within design specifications, ensuring optimal dewatering.
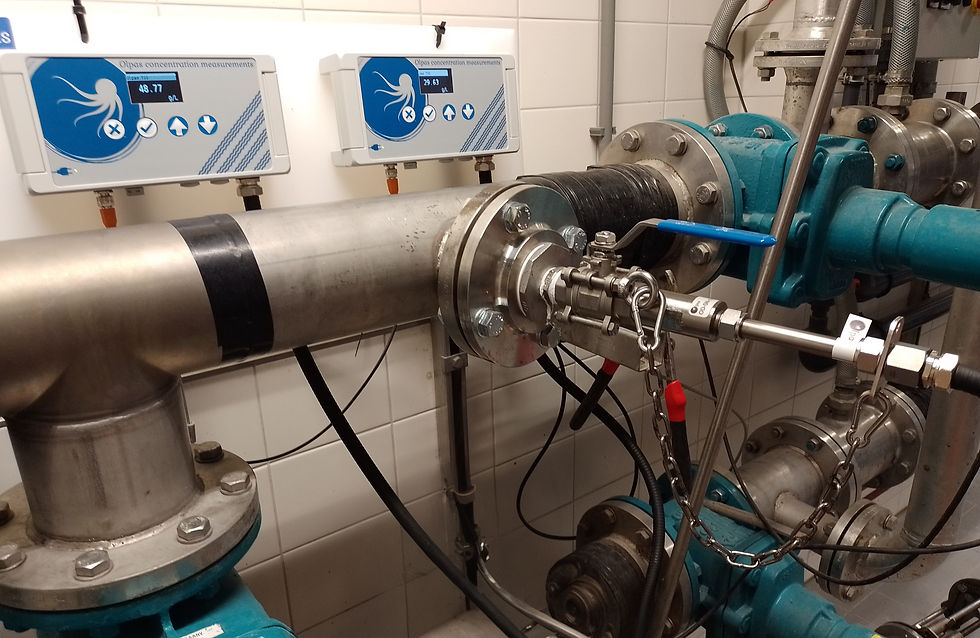
Above you can see one of our sensors in action, measuring at the inlet of a Dutch sludge dewatering.
This is our second post in a series about sludge dewatering, and the different measurements possible for optimisation of this expensive (in energy and chemicals used) process.
Post 2: Feed-forward control as optimization strategy: using the sludge inlet concentration measurement for precise control decanter loading and PE dosing. (That's this post)
Post 3: Centrate/filtrate residuals measurement as a feedback loop on polymer dosing and efficiency
Post 4: Why sludge cake dry solids content is invaluable for large scale dewatering installations
Post 5: Let’s recap: why optimization of your process is necessary. Cutting operational cost and running a plant efficiently.
